Building with Bales
Straw bale buildings are nothing new, having existed since the late 1800s. However, their use declined from the 1940s to the 70s due to the popularity and ease of concrete construction. After rediscovery and revival in the 1980s, the method continues to be refined amongst environmental building advocates.
Today, buildings and the construction sector account for 39% of the world's carbon emissions. One of the major culprits is concrete, estimated to be responsible for at least 8% of global emissions. Straw, by comparison, is low in embodied energy, a natural carbon sequesters and only has a 1-year growth cycle. A bale is approximately 40% carbon by weight, and its cellulose structure (like wood) makes it incredibly insulative and naturally fire-retardant*. If kept dry, straw can last hundreds to thousands of years.
*The denser (compressed) the bale, the more fire resistant. Tests show an earth-rendered wall can hold for 1 hour.
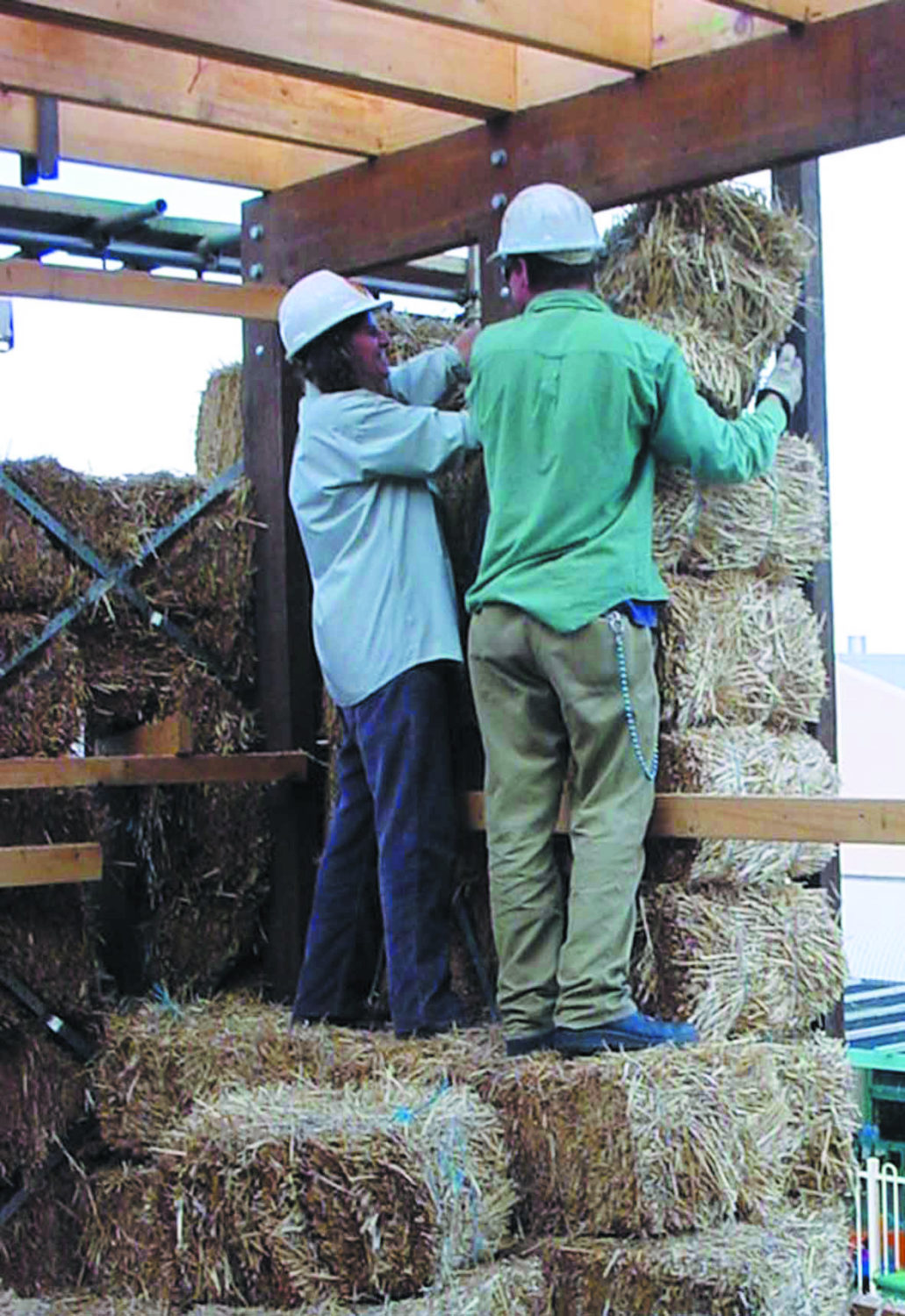
The ease of straw bale construction lends itself to self build projects (image credit Paul Downton)
The beauty of bales is the low cost and the limited processing needed. Bales come pre-compressed from farms and, once on-site, only need to be compressed a further 10% before use. The two methods to build with bales are:
1. as the structural load-bearing component of a wall (much like bricks)
2. as fill for a wall cavity (non-load bearing)
Bale walls are tied with bamboo or wood pins and plastered with a lime-based or earth/clay render. Most failures in bale buildings are directly related to moisture intrusion; bales must therefore sit about 300-450mm off the ground to stop water ingress, typically on a foundation of repurposed car tyres rammed with gravel; however, more traditional foundations also work.
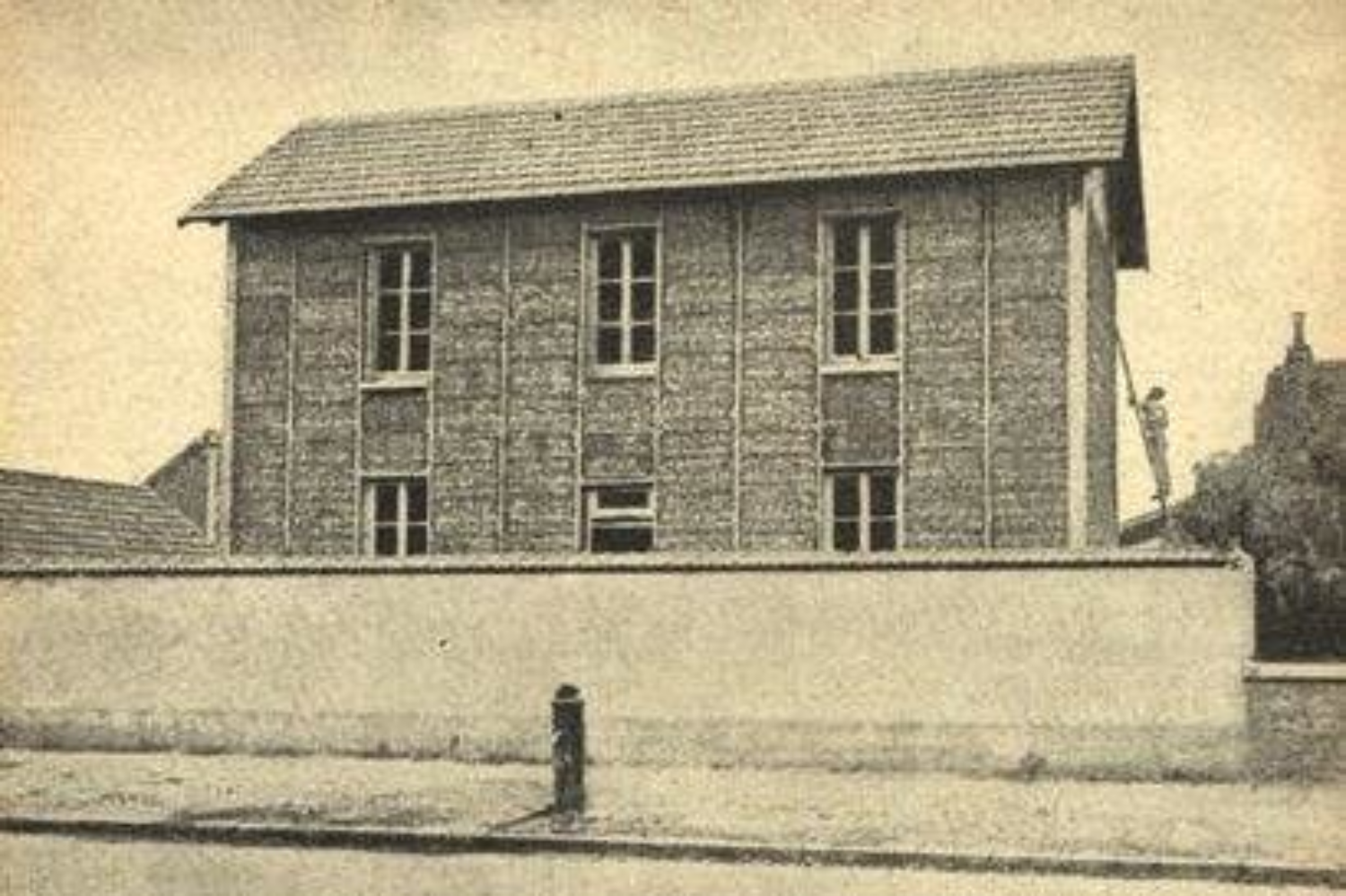
The Feuillette House in France was built in 1921 by a French engineer looking for new and cheaper construction methods, as a response to the housing crisis caused by World War I (image credit The Last Straw)
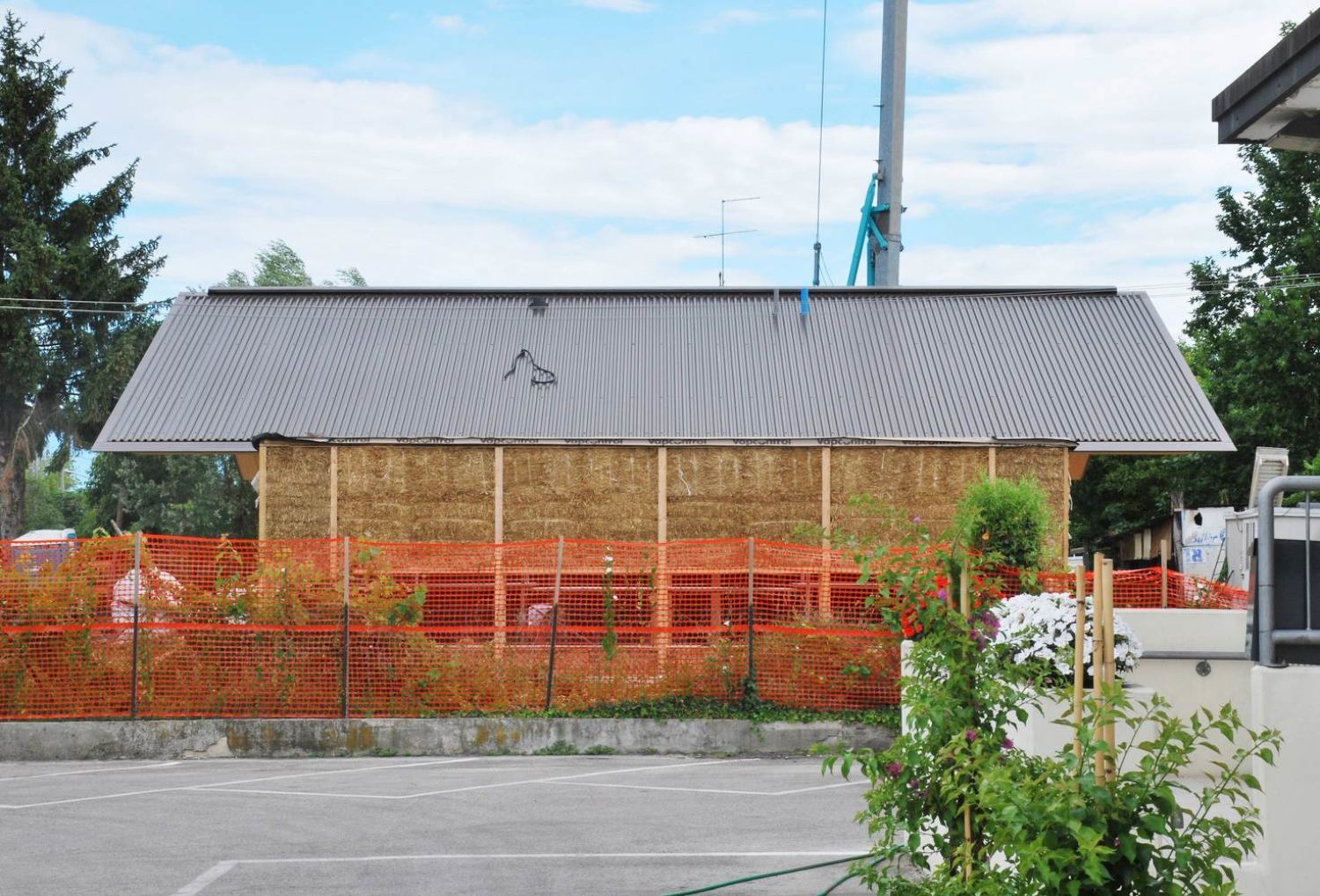
SCL Straw-Bale House under construction, Jimmi Pianezzola Architetto (© Alberto Sinigaglia)
Despite growing enough straw to build approximately 600,000 houses, the UK only constructs around 100,000 bale buildings a year. On projects such as Tendring Colchester Borders Community Garden, where Periscope is working on a 7,500-home masterplan on 715ha, of which approximately 30% is arable farmland, straw could be a game changer. Existing farms have the potential to grow and bale straw on-site, reducing construction travel and skilling local people in sustainable building methods. Additionally, there is scope to streamline construction further through prefabrication, with on-site factories producing straw wall cassettes, engineered to seamlessly slot together.
As we search for more sustainable construction materials, the possibilities of straw are (almost) endless.
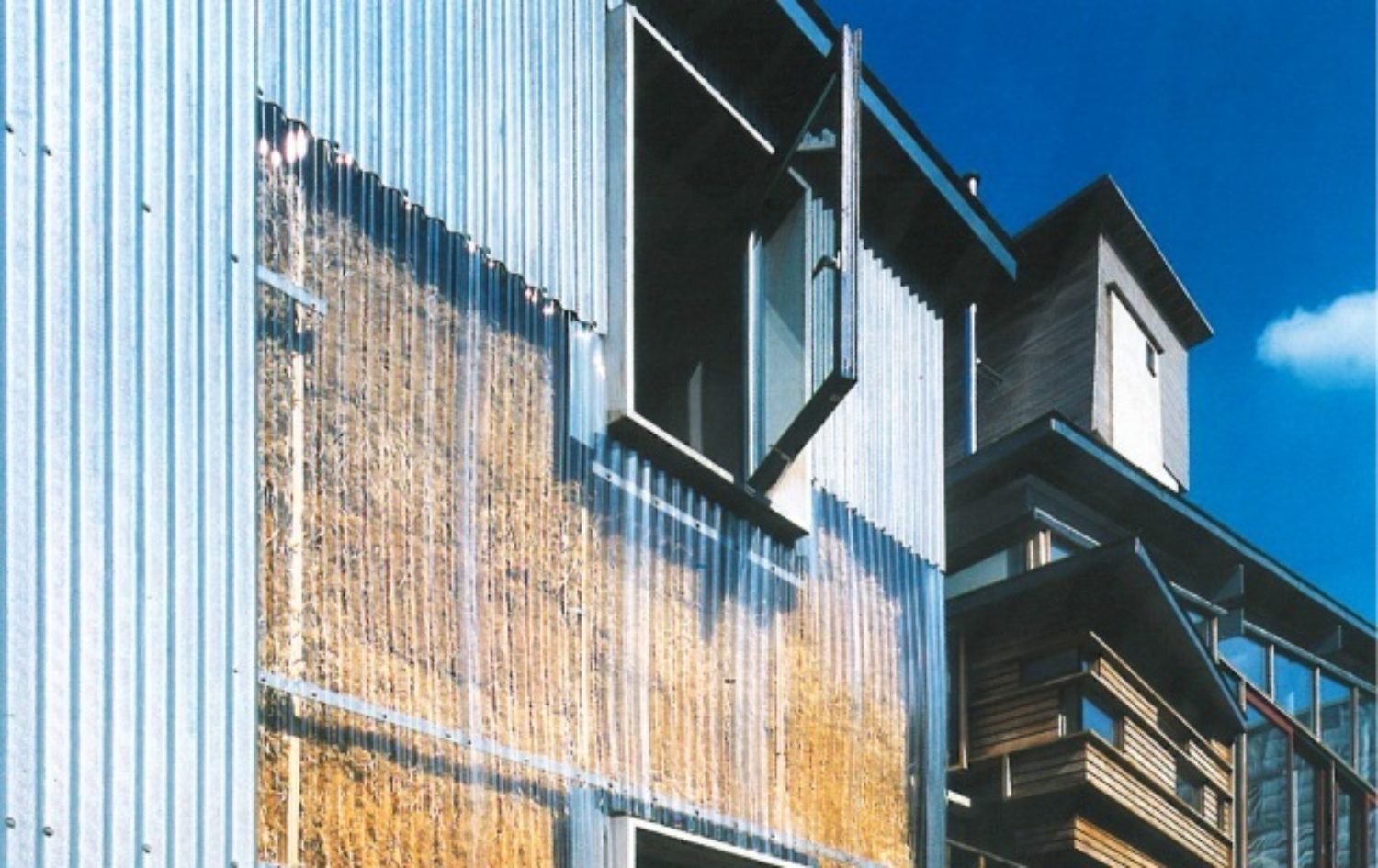
The straw Bale House in London, where the use of straw is celebrated and on-show (© Sarah Wigglesworth)
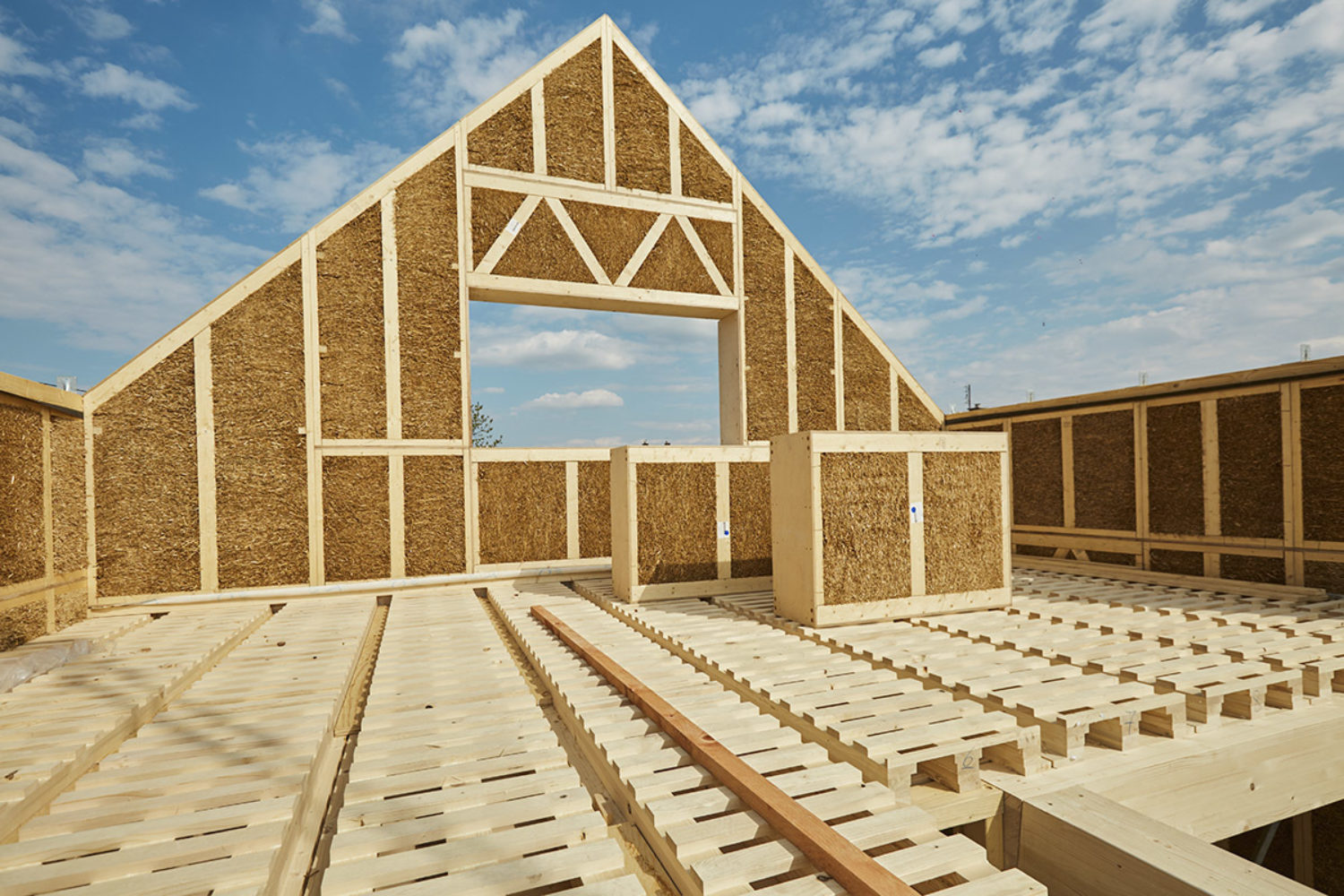
Prefabricated cassette construction (© EcoCocon)